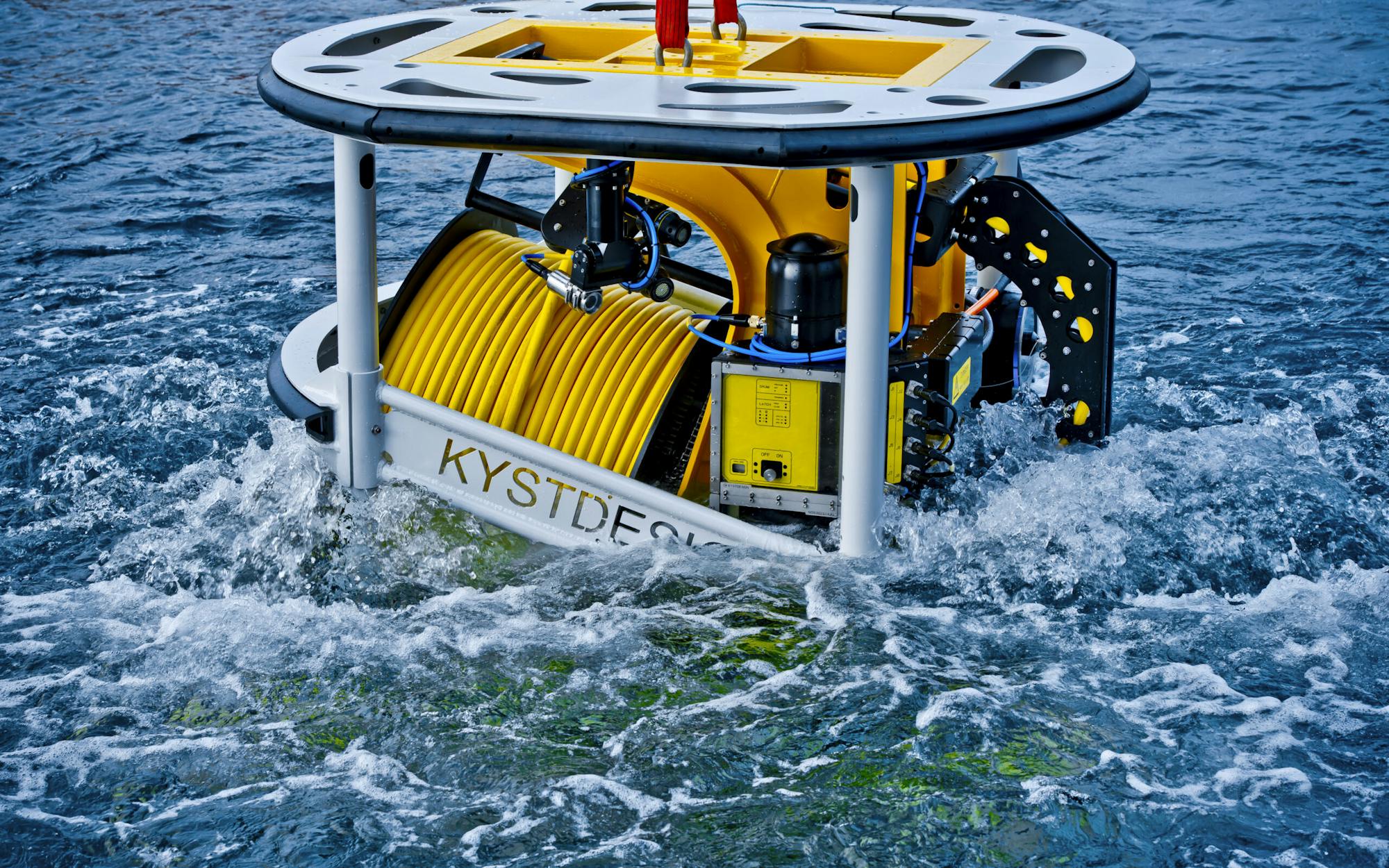
TMSs generally receive little attention compared to ROVs, but they are still an important element for achieving efficient and safe ROV operations.
Original version of this article was printed in the Norwegian magazine DYP, available here: ffu-nr-2-2024-lav-sider.pdf (dbs87poc94jww.cloudfront.net).
What is a TMS
A TMS, or Tether Management System, is a subsea winch with a nearly weight-neutral cable, the primary purpose of which is to give the ROV the greatest possible freedom for manoeuvring and job execution. The TMS and ROV are launched and lowered to working depth using a steel-reinforced lifting cable. On some occasions, it is appropriate to operate the ROV without using a TMS, such as in connection with seabed mapping and pipe inspection where highest possible speed over long distances is crucial. In such cases, the ROV operates with a large offset to the mother vessel, which makes the use of TMS challenging. For most missions with work-class ROVs, the use of TMS is important for many reasons.
Why TMS
It goes without saying that for an ROV that is to perform delicate operations with a manipulator or other tools, it is important to have the greatest possible stability and freedom for manoeuvring, especially if you are going into structures or other places with difficult access. The fact that the ROV can use its forces for positioning instead of pulling on a heavy steel-reinforced cable has major advantages.
Operations with TMS also increase safety, especially in connection with launching and recovery operations. The ROV is approximately weight-neutral in water, when it hits the water it will initially float. It is then a great advantage with TMS, which often weighs 2-3 tons in water. The TMS will quickly press the ROV down into the water and reduce the risk of slack lifting cable with the resulting unwanted snap forces in the cable. Furthermore, the TMS will contribute to getting down to working depth faster, which can contribute to significant time savings, especially in connection with deep-sea operations down to 6000m sea depth.
Hydraulic vs. Electric TMS
Kystdesign is currently testing out its two newly developed electric TMSs which are part of the ZEEROV systems to be mobilized on the new USVs, unmanned surface vessels, to Reach Subsea. These TMSs are very compact to be used on board the USV vessels which are only 24m long. Kystdesign has previously developed TMS with hydraulic motors for drum drive, tension wheel and latch, but for this delivery it was too big, and we had to think anew. The interaction between drum drive and tension wheel is important to achieve gentle handling of the cable, as well as correct winding on the drum. It is also important that you have enough power to pull in a possibly “dead” ROV, but at the same time it should have a load limit so that it winds out if this limit is exceeded. This shows that interaction and correct configuration of the motors are crucial for good operational safety and long cable life. And this is where the electric motors come into their own, as they have several regulatory technical advantages that hydraulic motors do not have. The inverter controls that we have developed for both thrusters and TMS motors provide full control of both speed and moments, which provides better regulation options compared to the use of hydraulic motors and valves. As an extra safety measure, we have a load cell on all our TMSs that continuously measures tensile force in the cable. This was originally intended as a safety function, but in practice this is something the operators actively use to assess the need for in/out winding of the tether in the operation.
Future TMS
Kystdesign has found that working towards various subsea industries can be very developing. Deliveries to marine research make up a small part of our turnover, but at the same time constitute a significant driver for our technology. The biggest technological leap marine research has contributed to is the further development of ROV and TMS adapted for operations down to 6000m depth. Other functionality that has come through this collaboration is a tool drawer on TMS as well as light and camera booms on the TMS frame that enable observation of ROV operations from a bird’s eye view.
As it becomes more common to operate the ROVs from a control centre on land and that the ROVs can also operate from unmanned boats for long periods without supervision, the market for a tool magazine on the TMS may become even more relevant.
As mentioned earlier, TMS perhaps undeservedly receives little attention compared to ROV. Today it is an important piece for carrying out successful ROV operations. Perhaps it could become an even more important factor for streamlining future ROV operations.
Kystdesign’s vision is to “simplify and improve global ROV operations”, the TMS is definitely an important element in this context.